Zementherstellung: Unterschied zwischen den Versionen
Keine Bearbeitungszusammenfassung |
Keine Bearbeitungszusammenfassung |
||
Zeile 1: | Zeile 1: | ||
[[Datei:Zementherstellung.jpg|mini|gerahmt|Zementherstellung (Trockenverfahren)]]Die wichtigsten Grundstoffe für die Zementherstellung sind [[Kalkstein]] und Ton, die meist getrennt abgebaut und danach im geeigneten Verhältnis gemischt werden. | [[Datei:Zementherstellung.jpg|mini|gerahmt|Zementherstellung (Trockenverfahren)]]Die wichtigsten Grundstoffe für die Zementherstellung sind [[Kalkstein]] und [[Ton]], die meist getrennt abgebaut und danach im geeigneten Verhältnis gemischt werden, aber auch als [[Mergel]] natürlich gemischt vorliegen. | ||
Die Zementherstellung umfasst fünf Hauptbereiche: | Die Zementherstellung umfasst fünf Hauptbereiche: |
Version vom 7. Juli 2015, 12:12 Uhr
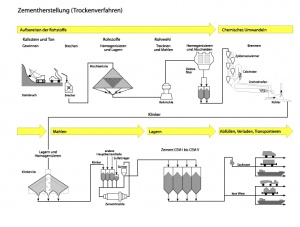
Die wichtigsten Grundstoffe für die Zementherstellung sind Kalkstein und Ton, die meist getrennt abgebaut und danach im geeigneten Verhältnis gemischt werden, aber auch als Mergel natürlich gemischt vorliegen.
Die Zementherstellung umfasst fünf Hauptbereiche:
1. Gewinnung und Aufbereitung des Rohmaterials:
Lockerung des Gesteins im Sprengverfahren und Verladung mit Löffelbaggern oder Radschaufelladern auf Schwerlastwagen. In einer Brecheranlage zerkleinert und zu Schotter. Aufschüttung von Mischbetten zum Ausgleich grober Schwankungen der Rohstoffe. Der Calciumcarbonatgehalt sollte 76 bis 78 % der Mischung betragen. Zugabe von Korrekturstoffen (Sand, Löß, Eisenoxid), um das Verhältnis von Siliciumdioxid (SiO2) zu Tonerde (Al2O3) und Eisenoxid (Fe2O3) in engen Grenzen zu halten. Mahlen und Trocknen der Rohmischung in Mahltrocknungsanlagen (Rohrmühlen mit Füllung aus Stahlkugeln oder Wälzmühlen mit Stahlwalzen). Dabei werden ca. 90 % des Mahlguts zu Körnern unter 90 µm Größe vermahlen. Das fertige Mahlgut (Rohmehl) wird in hintereinandergeschalteten Silos durch systematisches Abziehen und Befüllen "homogenisiert", d.h. innig und gleichmäßig vermischt.
2. Brennen des Zementklinkers:
Das Brennen erfolgt in einem Drehofen von mehreren Metern Durchmesser und 50 bis 200 Metern Länge. Die Öfen rotieren langsam um ihre Längsachse. Infolge eines leichten Gefälles wandert das an einem Ende eingegebene Rohmehl der Flamme am anderen Ende des Ofens entgegen. Öfen mit Zyklonvorwärmer (Schwebegas-Wärmetauscheröfen) besitzen einen Wärmetauscher, der aus einem System mehrerer Zyklone besteht, in denen das Rohmehl auf rd. 800 °C erhitzt wird. Am Ende des Drehofens – in der Sinterzone – wird das Brenngut auf 1400 bis 1450 °C erhitzt, es beginnt teilweise zu schmelzen (Sinterung). Aus den Ausgangsstoffen bilden sich dabei die so genannten Klinkerphasen. Das sind Calciumsilicate und Calciumaluminate, die dem Zement seine charakteristischen Eigenschaften bei der hydraulischen Erhärtung geben. Das Brennprodukt, der Zementklinker, verlässt den Ofen, wird gekühlt und gelangt zum Klinkerlager.
3. Mahlen der Zemente:
Damit aus dem Zementklinker das reaktionsfähige Produkt Zement entsteht, muss er äußerst fein gemahlen werden (Mahlfeinheit). Bei der Produktion von Portlandzementen wird der Zementmühle Zementklinker und etwa 5 M.-% Gips und/oder Anhydrit als Erstarrungsregler aufgegeben. Zur Erzeugung von Portlandhüttenzement und Hochofenzement werden die nach DIN EN 197-1 vorgeschriebenen Mengen Hüttensand zugemahlen. Auch bei anderen Zementarten werden Zementklinker und Zumahlstoffe in dem meist mehrstufigen Prozess i. d. R. gemeinsam gemahlen. Das fertige Mahlgut, der Zement, wird von den Zementmühlen zu den Zementsilos gefördert und gelangt von dort zu den Packmaschinen und zur losen Verladung.
4. Überwachung, Güteüberwachung:
Die Einhaltung der Zusammensetzung und der Eigenschaften des Zements wird durch die werkseigene Produktionskontrolle und die Fremdüberwachung überprüft. Gleichmäßige Eigenschaften des Zements werden durch weitgehend automatische Probennahme und Analyse der Roh-, Zwischen- und Endprodukte bei der Zementherstellung und entsprechende Steuer- und Regelmaßnahmen erreicht.
5. Umweltschutz:
Emissionen von Stäuben und Gasen sind durch verfahrenstechnische Umstellungen bei der Zementherstellung drastisch vermindert worden. Zu Beginn der 90er Jahre betrug der Anteil der Zementindustrie an der gesamten industriellen Staubemission rd. 1 %, bei Stickoxiden rd. 1,5 %. Eingriffe in die Natur durch Abbauflächen und Steinbrüche werden durch intensive Rekultivierung in land- und forstwirtschaftliche Nutzflächen, in Biotope oder in Freizeit- und Naherholungsgebiete abgemildert.