Zementmühle: Unterschied zwischen den Versionen
Keine Bearbeitungszusammenfassung |
Keine Bearbeitungszusammenfassung |
||
(6 dazwischenliegende Versionen desselben Benutzers werden nicht angezeigt) | |||
Zeile 1: | Zeile 1: | ||
[[Datei:Zementmuehle.jpg|mini|Prinzipien der Zerkleinerung mit Zementmühlen]] | [[Datei:Zementmuehle.jpg|mini|Prinzipien der Zerkleinerung mit Zementmühlen]] | ||
[[Mahlfeinheit]] und [[Korngrößenverteilung des Zements|Korngrößenverteilung]] sind wichtige Zementeigenschaften, die die [[Festigkeitsentwicklung]] des erhärtenden Zements und den [[Wasseranspruch]] bei der [[Hydratation]] beeinflussen. Beide Eigenschaften können durch die Art der eingesetzten Zementmühlen beeinflusst werden.<br> | [[Mahlfeinheit]] und [[Korngrößenverteilung des Zements|Korngrößenverteilung]] sind wichtige Zementeigenschaften, die die [[Festigkeitsentwicklung]] des erhärtenden Zements und den [[Wasseranspruch]] bei der [[Hydratation]] beeinflussen. Beide Eigenschaften können durch die Art der eingesetzten Zementmühlen beeinflusst werden.<br> | ||
Zum Herstellen des Zements wird der [[Zementklinker]] allein oder mit weiteren Hauptbestandteilen wie [[Hüttensand]], [[Puzzolane|Puzzolan]] | |||
oder [[Flugasche]] fein gemahlen. Dem Mahlgut wird beim Aufgeben in die Mühle Calciumsulfat als Erstarrungsregler zugegeben.<br> | |||
Die Mahlung von Zement mit mehreren Hauptbestandteilen kann in einer Mühle gemeinsam (gemeinsame Mahlung) oder aber getrennt nach den Bestandteilen in mehreren Mühlen erfolgen. Bei der gemeinsamen Mahlung reichert sich in der Regel die schwerer mahlbare Komponente im Grobbereich und die leichter mahlbare Komponente im Feinstbereich an. Beim getrennten Mahlen können die einzelnen Bestandteile gezielt auf die gewünschte Feinheit gemahlen werden. Die fertigen Zemente werden schließlich durch Mischen der gemahlenen Bestandteile erzeugt. <br> | |||
In den Anfängen der industriellen [[Zementherstellung]] verwendete man zum Vorzerkleinern der Rohstoffe und des [[Klinker|Klinkers]] Backenbrecher, zum Schroten Walzwerke und zum Feinmahlen Mahlgänge, die aus zwei aufeinander liegenden Mühlsteinen bestanden. Weitere Mahlaggregate waren u.a. der Kollergang zur Nassaufbereitung des Rohmaterials, verschiedene Bauarten der Walzmühle und die in den USA entwickelte Fliehkraft-Pendelmühle (Griffin-Mühle) zum Mahlen von Zement.<br> | In den Anfängen der industriellen [[Zementherstellung]] verwendete man zum Vorzerkleinern der Rohstoffe und des [[Klinker|Klinkers]] Backenbrecher, zum Schroten Walzwerke und zum Feinmahlen Mahlgänge, die aus zwei aufeinander liegenden Mühlsteinen bestanden. Weitere Mahlaggregate waren u.a. der Kollergang zur Nassaufbereitung des Rohmaterials, verschiedene Bauarten der Walzmühle und die in den USA entwickelte Fliehkraft-Pendelmühle (Griffin-Mühle) zum Mahlen von Zement.<br> | ||
Ziel der weiteren Entwicklung der Mahlaggregate war es vor allem, die Mahlfeinheit zu erhöhen und gleichzeitig die Durchsatzleistung zu steigern. Höhere Mahlfeinheiten bei ausreichenden Durchsatzleistungen | Ziel der weiteren Entwicklung der Mahlaggregate war es vor allem, die Mahlfeinheit zu erhöhen und gleichzeitig die Durchsatzleistung zu steigern. Höhere Mahlfeinheiten bei ausreichenden Durchsatzleistungen ergaben die ab 1892 in die deutsche Zementindustrie eingeführten Kugelmühlen, in denen in einem rotierenden Rohr Stahlkugeln im Freifall das Mahlgut zerkleinern. Bis 1920 hatten sie die anderen Mühlenbauarten sowohl für das Mahlen der Rohstoffe als auch des Zements verdrängt. Seit etwa 1985 werden zunehmend neben den Kugelmühlen auch Walzenmühlen und Wälzmühlen eingesetzt. Das eingesetzte Mahlsystem beeinflusst die [[Korngrößenverteilung]] des Fertigguts und damit dessen anwendungstechnische Eigenschaften. <br> | ||
In der Kugelmühle wird das Gut zusammen mit einer Stahlkugelfüllung in einem um seine Langsachse rotierenden, innen gepanzerten Rohr umgewälzt und dabei gemahlen. In der Vertikal-Wälzmühle überrollen ortsfest angebrachte Walzen das Mahlgut auf einem sich drehenden Teller. Die Horizontal-Wälzmühle (Horomill, Horizontal Roller Mill) besteht aus einem kurzen, horizontal gelagerten Mühlenrohr, auf dessen gepanzerte Innenwand eine gepanzerte Mahlwalze hydraulisch aufgepresst wird. In der Gutbett-Walzenmühle – auch Rollenpresse genannt - wird das Gut in dem Spalt zwischen zwei gegenläufig rotierenden Walzen durch Druck zerkleinert.<br> | |||
Bei den Mahlverfahren werden das '''Durchlaufmahlverfahren''' und das '''Umlaufmahlverfahren''' unterschieden.<br> | Bei den Mahlverfahren werden das '''Durchlaufmahlverfahren''' und das '''Umlaufmahlverfahren''' unterschieden.<br> | ||
Beim '''Durchlaufmahlverfahren''' besteht das Fertiggut aus dem Mühlenaustragsgut. Der wesentliche Vorteil von Durchlaufmahlanlagen mit Kugelmühlen ist ihr einfacher Aufbau, der eine hohe Betriebssicherheit bei geringem Wartungs- und Instandhaltungssaufwand verspricht. Im Vergleich mit anderen Mahlsystemen haben aber diese Anlagen den höchsten spezifischen Energiebedarf bzw. die niedrigste Energieausnutzung.<br> | Beim '''Durchlaufmahlverfahren''' besteht das Fertiggut aus dem Mühlenaustragsgut. Der wesentliche Vorteil von Durchlaufmahlanlagen mit Kugelmühlen ist ihr einfacher Aufbau, der eine hohe Betriebssicherheit bei geringem Wartungs- und Instandhaltungssaufwand verspricht. Im Vergleich mit anderen Mahlsystemen haben aber diese Anlagen den höchsten spezifischen Energiebedarf bzw. die niedrigste Energieausnutzung.<br> | ||
Für das Mahlen hochwertiger Zemente ist die einfache Durchlaufmahlanlage in der Regel nicht geeignet, da mit zunehmendem Zerkleinerungsfortschritt entlang der Mahlbahn die Agglomerationsneigung des Mahlguts zunimmt und der spezifische Energieaufwand überproportional mit der Feinheit ansteigt.<br> | Für das Mahlen hochwertiger Zemente ist die einfache Durchlaufmahlanlage in der Regel nicht geeignet, da mit zunehmendem Zerkleinerungsfortschritt entlang der Mahlbahn die Agglomerationsneigung des Mahlguts zunimmt und der spezifische Energieaufwand überproportional mit der Feinheit ansteigt.<br> | ||
Effizienter arbeiten '''Umlaufmahlanlagen'''. Hier wird das Mahlgut nicht in einem Mahlgang fertig gemahlen. Das aus der Mühle austretende Mahlgut wird in einem Sichter in Fertiggut und Griese getrennt. Die Griese gelangen zurück in den Mühleneinlauf und werden gemeinsam mit dem aufgegebenen Frischgut weiter zerkleinert. Das im Sichter abgeschiedene Produkt bildet mit dem Material aus dem Entstaubungsfilter das fertige Produkt. Im Allgemeinen unterscheidet man zwischen folgenden Arten | Effizienter arbeiten '''Umlaufmahlanlagen'''. Hier wird das Mahlgut nicht in einem Mahlgang fertig gemahlen. Das aus der Mühle austretende Mahlgut wird in einem Sichter in Fertiggut und Griese getrennt. Die Griese gelangen zurück in den Mühleneinlauf und werden gemeinsam mit dem aufgegebenen Frischgut weiter zerkleinert. Das im Sichter abgeschiedene Produkt bildet mit dem Material aus dem Entstaubungsfilter das fertige Produkt. Im Allgemeinen unterscheidet man zwischen folgenden Arten: | ||
* Umlaufmahlanlagen mit Kugelmühle | * Umlaufmahlanlagen mit Kugelmühle | ||
* Umlaufmahlanlagen mit Kugelmühle und Vorzerkleinerungsstufe | * Umlaufmahlanlagen mit Kugelmühle und Vorzerkleinerungsstufe | ||
Zeile 16: | Zeile 18: | ||
* Umlaufmahlanlagen mit Wälzmühlen | * Umlaufmahlanlagen mit Wälzmühlen | ||
==Siehe auch== | |||
[[Zerkleinerungstechnik]] | |||
== Literatur == | == Literatur == |
Aktuelle Version vom 15. Februar 2021, 12:41 Uhr
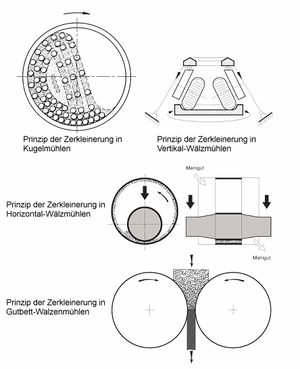
Mahlfeinheit und Korngrößenverteilung sind wichtige Zementeigenschaften, die die Festigkeitsentwicklung des erhärtenden Zements und den Wasseranspruch bei der Hydratation beeinflussen. Beide Eigenschaften können durch die Art der eingesetzten Zementmühlen beeinflusst werden.
Zum Herstellen des Zements wird der Zementklinker allein oder mit weiteren Hauptbestandteilen wie Hüttensand, Puzzolan
oder Flugasche fein gemahlen. Dem Mahlgut wird beim Aufgeben in die Mühle Calciumsulfat als Erstarrungsregler zugegeben.
Die Mahlung von Zement mit mehreren Hauptbestandteilen kann in einer Mühle gemeinsam (gemeinsame Mahlung) oder aber getrennt nach den Bestandteilen in mehreren Mühlen erfolgen. Bei der gemeinsamen Mahlung reichert sich in der Regel die schwerer mahlbare Komponente im Grobbereich und die leichter mahlbare Komponente im Feinstbereich an. Beim getrennten Mahlen können die einzelnen Bestandteile gezielt auf die gewünschte Feinheit gemahlen werden. Die fertigen Zemente werden schließlich durch Mischen der gemahlenen Bestandteile erzeugt.
In den Anfängen der industriellen Zementherstellung verwendete man zum Vorzerkleinern der Rohstoffe und des Klinkers Backenbrecher, zum Schroten Walzwerke und zum Feinmahlen Mahlgänge, die aus zwei aufeinander liegenden Mühlsteinen bestanden. Weitere Mahlaggregate waren u.a. der Kollergang zur Nassaufbereitung des Rohmaterials, verschiedene Bauarten der Walzmühle und die in den USA entwickelte Fliehkraft-Pendelmühle (Griffin-Mühle) zum Mahlen von Zement.
Ziel der weiteren Entwicklung der Mahlaggregate war es vor allem, die Mahlfeinheit zu erhöhen und gleichzeitig die Durchsatzleistung zu steigern. Höhere Mahlfeinheiten bei ausreichenden Durchsatzleistungen ergaben die ab 1892 in die deutsche Zementindustrie eingeführten Kugelmühlen, in denen in einem rotierenden Rohr Stahlkugeln im Freifall das Mahlgut zerkleinern. Bis 1920 hatten sie die anderen Mühlenbauarten sowohl für das Mahlen der Rohstoffe als auch des Zements verdrängt. Seit etwa 1985 werden zunehmend neben den Kugelmühlen auch Walzenmühlen und Wälzmühlen eingesetzt. Das eingesetzte Mahlsystem beeinflusst die Korngrößenverteilung des Fertigguts und damit dessen anwendungstechnische Eigenschaften.
In der Kugelmühle wird das Gut zusammen mit einer Stahlkugelfüllung in einem um seine Langsachse rotierenden, innen gepanzerten Rohr umgewälzt und dabei gemahlen. In der Vertikal-Wälzmühle überrollen ortsfest angebrachte Walzen das Mahlgut auf einem sich drehenden Teller. Die Horizontal-Wälzmühle (Horomill, Horizontal Roller Mill) besteht aus einem kurzen, horizontal gelagerten Mühlenrohr, auf dessen gepanzerte Innenwand eine gepanzerte Mahlwalze hydraulisch aufgepresst wird. In der Gutbett-Walzenmühle – auch Rollenpresse genannt - wird das Gut in dem Spalt zwischen zwei gegenläufig rotierenden Walzen durch Druck zerkleinert.
Bei den Mahlverfahren werden das Durchlaufmahlverfahren und das Umlaufmahlverfahren unterschieden.
Beim Durchlaufmahlverfahren besteht das Fertiggut aus dem Mühlenaustragsgut. Der wesentliche Vorteil von Durchlaufmahlanlagen mit Kugelmühlen ist ihr einfacher Aufbau, der eine hohe Betriebssicherheit bei geringem Wartungs- und Instandhaltungssaufwand verspricht. Im Vergleich mit anderen Mahlsystemen haben aber diese Anlagen den höchsten spezifischen Energiebedarf bzw. die niedrigste Energieausnutzung.
Für das Mahlen hochwertiger Zemente ist die einfache Durchlaufmahlanlage in der Regel nicht geeignet, da mit zunehmendem Zerkleinerungsfortschritt entlang der Mahlbahn die Agglomerationsneigung des Mahlguts zunimmt und der spezifische Energieaufwand überproportional mit der Feinheit ansteigt.
Effizienter arbeiten Umlaufmahlanlagen. Hier wird das Mahlgut nicht in einem Mahlgang fertig gemahlen. Das aus der Mühle austretende Mahlgut wird in einem Sichter in Fertiggut und Griese getrennt. Die Griese gelangen zurück in den Mühleneinlauf und werden gemeinsam mit dem aufgegebenen Frischgut weiter zerkleinert. Das im Sichter abgeschiedene Produkt bildet mit dem Material aus dem Entstaubungsfilter das fertige Produkt. Im Allgemeinen unterscheidet man zwischen folgenden Arten:
- Umlaufmahlanlagen mit Kugelmühle
- Umlaufmahlanlagen mit Kugelmühle und Vorzerkleinerungsstufe
- Umlaufmahlanlagen mit Gutbettwalzenmühlen
- Umlaufmahlanlagen mit Wälzmühlen
Siehe auch
Literatur
- Verein Deutscher Zementwerke e.V. (VDZ): Merkblatt Vt18 - Zerkleinerung. Düsseldorf 2020
- Zement-Merkblatt B1: Zemente und ihre Herstellung
- Locher, Friedrich W.: Zement – Grundlagen der Herstellung und Verwendung. Verlag Bau+Technik GmbH, Düsseldorf 2000